AI is revolutionizing every aspect of work. Some of these tools are extremely well-known – everyone’s talking about ChatGPT and Midjourney. But those are just the most visible examples. They’re also pretty new, so they’re subjects of hot debate. If you look deeper, you’ll see that AI has been around for a while, and it’s already had a huge impact on American industry.
Manufacturing is a prime example. Today, 93% of industry leaders say they’re already using some form of AI (AI Multiple Research). From predictive maintenance and quality control to robots and smart factories, this technology is everywhere – and it’s going to change the very nature of work.
What AI Manufacturing Tools Mean for the Labor Market
As AI technology grows more powerful and popular, U.S. workers are expressing concern. What do these tools mean for the job market? Will machines replace human workers? Your employees might be concerned about the future, especially in the manufacturing industry. Companies are indeed starting to automate routine and repetitive tasks that workers used to perform. However, the impact of AI on the labor market is more nuanced than it might seem.
We’re facing an unprecedented labor shortage. As of 2024, there are 8.8 million job openings in the U.S. and just 6.5 million unemployed people (U.S. Chamber of Commerce). Manufacturers are getting hit especially hard. Experts predict that by 2030, there could be 2.1 million unfilled jobs in that industry alone (National Association of Manufacturers).
HR teams are already scrambling to revamp their recruiting strategies, hoping to attract young workers with a new focus on career development and on-the-job training. This strategy shows new hires that you’re invested in their growth, encouraging long-term employee loyalty. Over time, that should save on recruiting costs and help companies maintain institutional knowledge. But it won’t solve the bigger problem: as Baby Boomers retire, there will just be fewer workers available. From that perspective, AI tools aren’t here to take away jobs. They’re here to fill in the gaps.
Of course, that’s just one side of the story. AI is also changing the type of work that businesses perform. A company might not need employees to pack boxes anymore – but it will need people to service AI tools. That could mean data analysts, robotics programmers, and other technicians. This could be a global opportunity to upskill the workforce.
AI and HR: Supporting the Transition
Fortunately, most employees want the same thing their employers need: learning and development. One survey found 94% of employees would stay at a company longer if it offered training opportunities (Zippia). That’s where HR comes in.
Upskilling is the key to success for all involved, from the C-Suite to entry-level employees. In one fell swoop, HR leaders can boost employee engagement, improve retention rates, and drive business success. The future is uncertain. It could bring new technologies, industry disruptions, a continuing labor shortage, or all of the above. With a more agile, curious, loyal team, you’ll be better prepared for whatever comes next.
AI is also changing the nature of work for HR professionals. Before you can upskill employees, you have to hire them. AI-powered recruiting software streamlines that process, helping you write job descriptions, post on multiple job boards, and communicate with candidates. These tools also have a major impact on your pipeline. They can identify passive candidates and interrupt implicit bias, dramatically expanding your talent pool. As the labor shortage makes recruiting more competitive, these tools will become the baseline. If you want to attract top candidates, you’ll need to keep up with these rapidly changing trends.
Recruiting tools are just the tip of the iceberg. We can expect more AI-powered software to roll out soon, affecting not just HR but every area of business. In manufacturing, certain AI tools already have a major impact.
Types of AI in Manufacturing
Let’s take a look at some of AI’s top use cases in the manufacturing industry.
- Generative Design: Generative AI tools allow engineers to design products more efficiently, without sacrificing human creativity. These tools could save countless hours for designers and product testers required to meet rigorous specifications.
- Defect Detection: It doesn’t matter how well your product is supposed to work, clients and consumers need it to actually work well, every single time. Just a few defective inventory items can lead to an avalanche of bad reviews and lost trust. AI-powered defect detection analyzes visual and sensor data to ensure products meet quality standards.
- Predictive Maintenance: AI can monitor equipment performance, analyze sensor data, and predict when a machine might fail. This proactive approach prevents costly breakdowns, unplanned downtime, and – most importantly for HR – workplace incidents and injuries.
- Robotics and Automation: Advanced robots are transforming factory floors. Some collaborative robots work alongside human workers, increasing efficiency and safety. For instance, Amazon uses robots to identify store inventory, move items around the warehouse, and consolidate orders for delivery.
Smart Factories Take AI to the Next Level
What if you built a factory combining all these AI innovations? Some companies already have. They’re called smart factories (or intelligent factories, or digital factories) and they’re getting more common all the time. Smart factories integrate technologies like cloud computing, robotics, AI, and more to create fully automated production lines.
In a smart factory, every machine is equipped with complex sensors that collect information about their performance. AI algorithms collect data in real-time so they can identify patterns, predict issues, and make informed decisions about what to do next. The entire facility is interconnected, and all its systems can communicate seamlessly. Smart factories have several benefits:
- Efficiency: Between automation, predictive maintenance, and reduced downtime, smart factories are extremely efficient. They also allow production to scale quickly based on demand. This rapid adaptation to market changes is a significant competitive advantage.
- Product Quality: Advanced quality control, including AI-powered defect detection, improves the quality of finished products. Better products make customers happier and cut down on waste.
- Safety: Smart factories are safer for a few reasons. First, robots can do dangerous tasks that people would rather avoid. Second, AI-powered systems can monitor potential risks and resolve them before putting human workers in harm’s way.
Many smart factories still depend on human labor. That might always be true, but the rapid growth of technology makes it hard to predict the future. One thing is already clear: the advent of new AI tools is going to have a major impact on the nature of work.
How Paycor Helps
Whether you’re redesigning your factory layout or your HR strategy, there’s a lot of change on the horizon. Paycor’s tools automate repetitive tasks, giving you more time to focus on the big picture. From payroll to scheduling to benefits administration, our integrated solutions can support every aspect of HR.
Paycor’s suite of HR software empowers leaders to develop winning teams. Tools like Talent Management Software are purpose-built for you to coach, develop, upskill, and reward employees. With Paycor, you can help everyone on your team prepare for the future.
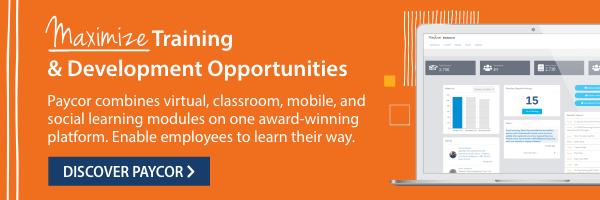