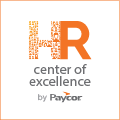
HR COE
Articles
Article
Article
Read Time: 8 min
Absence Management for Small Business – Best Practices
Absences can be costly for businesses. Understand the causes and see how to create an absence policy, here.
Article
Read Time: 7 min
How to Navigate Remote Training for the Work-from-Home Crowd
Keeping remote teams trained and equipped with information can be challenging. See how to optimize your training program.
Article
Read Time: 11 min
The Top Payroll Questions Answered for Employers
Keeping compliant with payroll regulations can be a tough challenge. But we’ve got you covered with our in-depth payroll Q&A. Read it now.
Article
Read Time: 8 min
What to Consider When Buying an Employee Time Clock
Employers need time clocks that are reliable and can report data into their payroll system. See all you need to consider before you spend a dime.
Article
Read Time: 7 min
What is the Role of HR in Succession Planning?
Employees leave critical roles regularly, and it’s up to HR to have a succession plan in place. See how your HR team can navigate the challenge.
Article
Read Time: 8 min
What is Talent Development?
You need a payroll system that works with your business. Get the facts on what you should consider during the evaluation process.
Article
Read Time: 11 min
Five Action Steps for a More Positive Work Culture
Organizations with a positive work culture attract more talent and increase productivity. See the steps to creative a strong culture at your organization.
Article
Read Time: 8 min
Employee Ghosting: Why it Happens and How Recruiters Can Avoid It
Often times job candidates have more than one option and may “ghost” an organization during an interview process. Learn about the root causes of ghosting and how to avoid it.
Article
Read Time: 7 min
ICHRA Rules: What are Individual Coverage HRAs?
An Individual Coverage Health Reimbursement Arrangement is now available for organizations of all sizes. See how an ICHRA can help your employees.
Article
Read Time: 8 min
Difference Between Mission and Vision Statement, Core Values & Goals
Core values, mission statements and goals can get commingled. Understanding their differences can help strategic planning. Get started here.
Article
Read Time: 16 min
OKR: Objectives and Key Results FAQs 2021
If you like the idea of implementing OKRs for your workplace, but aren’t sure where to start, we’ve got strategic guidance here. Start your planning today.